Discover the Benefits of Biaxial Fiberglass Tape in Industrial Applications
By:Admin
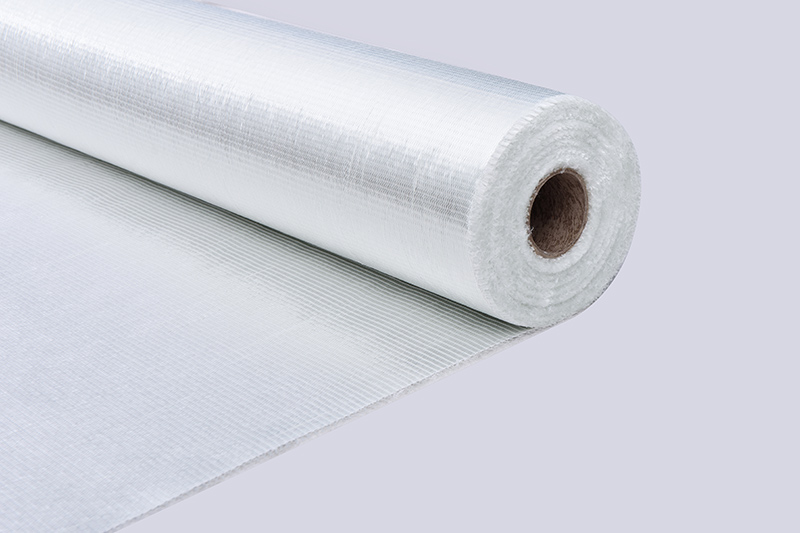
Biaxial Fiberglass Tape is a type of reinforced adhesive tape that has been gaining popularity in recent years for its superior strength and durability. It is specially designed for applications where a high level of strength and flexibility is required, making it ideal for use in a variety of industries, including construction, automotive, aerospace, and marine. This article will explore the features and benefits of Biaxial Fiberglass Tape and how it is revolutionizing the way we build structures.
Biaxial Fiberglass Tape is made up of several layers of fiberglass fabric, which are coated with a high-performance adhesive. The tape is then biaxially oriented, meaning that it is stretched in two different directions to create a cross-hatch pattern. This process creates a tape that is strong and flexible, capable of withstanding high loads and stresses while also allowing for expansion and contraction due to temperature changes.
One of the most significant advantages of Biaxial Fiberglass Tape is its outstanding strength-to-weight ratio. This means that it is much stronger than traditional materials while being much lighter in weight. This property makes it an excellent choice for applications where weight is a critical factor, such as in aerospace and automotive industries. Biaxial Fiberglass Tape is also highly resistant to corrosion, making it ideal for use in harsh environments, such as marine structures.
Another benefit of Biaxial Fiberglass Tape is its ease of use. It can be applied to a variety of surfaces, including metal, plastic, and composite materials, using standard application techniques. This makes it a versatile solution that can be used in a wide range of applications, from simple repairs to complex structural projects.
Biaxial Fiberglass Tape is also highly customizable, with different combinations of fiberglass fabrics, adhesive types, and tape widths available to suit specific project requirements. This can help to reduce waste and increase efficiency, as only the necessary amount of tape is used. The tape can also be pre-cut to specific lengths, making it quick and easy to apply.
One of the most significant advantages of Biaxial Fiberglass Tape is its ability to provide long-lasting protection against wear and tear. Unlike traditional materials like steel, which can corrode and weaken over time, Biaxial Fiberglass Tape is highly resistant to damage, making it an excellent choice for applications where long-term structural integrity is essential.
At () (remove brand name), we have been at the forefront of Biaxial Fiberglass Tape innovation for over a decade. Our team of experts has developed a range of high-quality tapes that are designed to meet the needs of our customers in a variety of industries. We use only the highest quality materials and manufacturing processes, ensuring that our tapes are of the highest quality and built to last.
Our Biaxial Fiberglass Tape products are highly versatile, with a range of widths, thicknesses, and adhesive types available to suit a wide variety of applications. We also offer custom tape cutting services, allowing our customers to get the exact amount of tape they need for their project.
In addition to our tape products, we also offer a range of technical support services, including consultations, training, and on-site support. Our team of experts can help you to select the best tape product for your project, as well as provide guidance on application techniques and best practices.
With its superior strength, durability, and ease of use, Biaxial Fiberglass Tape is quickly becoming the go-to solution for a wide range of industries. Whether you are repairing a boat, building a new structure, or designing the next generation of aerospace components, Biaxial Fiberglass Tape can help you to achieve outstanding results. Contact us () remove brand name) today to learn more about our Biaxial Fiberglass Tape products and how we can help you to build a stronger future.
Company News & Blog
New lightweight material made of carbon kevlar hybrid fabric is set to revolutionize the aerospace industry
Title: Innovative Carbon Kevlar Hybrid Fabric Revolutionizes the Textile IndustryIntroduction:In a groundbreaking development, an industry-leading company has introduced a cutting-edge Carbon Kevlar Hybrid Fabric, emerging as a game-changer in the textile world. Embracing advanced technologies, this revolutionary fabric combines the remarkable properties of carbon fiber and Kevlar, offering unprecedented strength, durability, and versatility. With its wide range of applications, this innovative fabric is set to reshape industries such as aerospace, automotive, sports, and defense.1. The Unparalleled Strength of Carbon Kevlar Hybrid Fabric:The Carbon Kevlar Hybrid Fabric incorporates the best qualities of both carbon fiber and Kevlar. Carbon fiber is renowned for its exceptional strength-to-weight ratio, making it a preferred choice in industries where lightweight yet robust materials are required. On the other hand, Kevlar is famous for its outstanding resistance to impact and abrasion, making it an ideal choice for ballistic protection and structural reinforcement. By combining these two fibers, this hybrid fabric transcends the limitations of conventional materials, ensuring enhanced performance in a variety of applications.2. Aerospace Industry: Empowering High-performance StructuresThe aerospace industry stands to benefit immensely from the introduction of Carbon Kevlar Hybrid Fabric. Due to its lightweight nature and superior strength, the fabric can be incorporated into the manufacture of aircraft components, including fuselages, wings, and engine parts. By utilizing this innovative fabric, manufacturers can significantly reduce the weight of aircraft, contributing to improved fuel efficiency and lower operating costs. Moreover, the exceptional fatigue resistance of the hybrid fabric enhances the durability and longevity of key structural elements, ensuring increased safety for passengers and crew.3. Automotive Industry: Paving the Way for Safer VehiclesIn the automotive sector, the integration of Carbon Kevlar Hybrid Fabric presents significant advancements in safety and performance. By utilizing this fabric for manufacturing body panels, car manufacturers can enhance crashworthiness while reducing overall vehicle weight. The superior impact resistance of the fabric combined with its lightweight attributes makes it a valuable asset in protecting passengers during collisions. As a result, vehicles can achieve better fuel efficiency while offering enhanced safety to occupants.4. Sports Industry: Elevating Performance EquipmentThe sports industry is no stranger to materials that offer exceptional strength and durability. The Carbon Kevlar Hybrid Fabric is set to revolutionize sports equipment, enabling athletes to reach new heights of performance. Sports gear, such as helmets, paddles, and protective gear, created using this hybrid fabric will offer unrivaled protection without compromising agility. The lightweight nature of the fabric will facilitate better maneuverability, giving athletes a competitive edge in various sports.5. Defense Industry: Reinforcing Military ApplicationsThe defense sector, where protection and reliability are paramount, can greatly benefit from the introduction of Carbon Kevlar Hybrid Fabric. The fabric's exceptional resistance to extreme temperatures and impact makes it an ideal choice for the manufacture of protective clothing and equipment for military personnel. As a result, soldiers will experience significantly improved protection without being encumbered by heavy gear.Conclusion:The introduction of Carbon Kevlar Hybrid Fabric represents an exciting milestone in the textile industry. This innovative fabric's ability to combine the extraordinary properties of carbon fiber and Kevlar opens up endless possibilities across various sectors. From aerospace to sports, and automotive to defense, this versatile fabric promises to redefine the standards of strength, durability, and performance. With its numerous benefits, the adoption of Carbon Kevlar Hybrid Fabric is set to revolutionize manufacturing processes and shape the future of the textile industry.
Revolutionary Lightweight Carbon Fiber Plain Unveiled in Latest Technology News" - "New Lightweight Carbon Fiber Plain Unveiled in Latest Tech News
Carbon Fiber Plain is one of the most versatile and high-strength materials in the world. With its unique properties, it has been used in industries ranging from aerospace to automotive, and even high-performance sports equipment. While many companies produce carbon fiber, (brand name) stands out as a leader in the field. Founded in XXXX, (brand name) has made it a mission to produce high-quality carbon fiber products with unmatched precision and quality. Despite being a relatively new player in the market, they quickly established themselves as a global leader in the field, serving clients in a wide variety of industries from all over the world.At (brand name), the production process begins by sourcing only the highest-quality raw materials available. The fibers are then woven together into the desired pattern, coated with a resin binder, and cured at high temperatures to create a strong composite. (Brand name) has invested heavily in state-of-the-art manufacturing equipment and processes to ensure that each product is of the highest quality and consistency.One of the biggest advantages of carbon fiber is its strength-to-weight ratio. Compared to traditional materials like steel or aluminum, carbon fiber can be up to ten times stronger while being significantly lighter. This has made it a popular choice for aerospace and automotive applications, where reducing weight without sacrificing strength is critical.Another benefit of carbon fiber is its durability. Unlike other materials that can be prone to corrosion or fatigue, carbon fiber is highly resistant to both. It is also non-conductive, making it an ideal choice for applications where electromagnetic interference could be an issue.Perhaps most impressively, carbon fiber can be molded into virtually any shape or geometry, giving designers and engineers unparalleled flexibility in creating products. From aircraft components to bicycle frames, the possibilities are endless.(Brand name) offers a wide variety of carbon fiber products, including sheets, tubes, and rods. They also work closely with clients to develop custom solutions to meet their specific needs. This level of flexibility and customization has helped to set (brand name) apart from the competition.One particularly exciting use of carbon fiber is in the field of renewable energy. Wind turbine blades, which are exposed to a wide range of environmental stresses, are often made from carbon fiber due to its strength and durability. This has helped to increase the efficiency and reliability of wind power generation, contributing to the transition to a more sustainable energy future.Carbon fiber has also found its way into the world of sports equipment. From tennis rackets to ski poles, carbon fiber is a popular choice due to its light weight and stiffness. Athletes around the world use carbon fiber equipment to help them perform at their best.In conclusion, (brand name) is a global leader in the production of high-quality carbon fiber products. Their dedication to precision and quality has helped them to establish themselves as a trusted partner for clients in a diverse range of industries. With the continued growth in applications for carbon fiber, (brand name) is poised to play an important role in shaping the future of many industries.
Nonwoven Activated Carbon Filter Cotton for Functional Fabric Applications
New Fabric Technology: Nonwoven Activated Carbon Filter CottonFabric technology has come a long way from being just a means to cover the body. Today, it has evolved to include functional fabrics that provide additional benefits to the wearer. One such fabric technology is nonwoven activated carbon filter cotton, which is quickly gaining popularity in the market for its ability to filter harmful substances and protect the wearer from pollution.Ruibang, a leading brand in the industry, has introduced a new product called the AC05-01 nonwoven activated carbon filter cotton. This product is made of a combination of activated carbon cloth, melt-blown nonwoven fabric, and carbon fiber cloth. The activated carbon cloth has a strong adsorption capacity, which effectively filters out harmful substances such as odors and gases. The melt-blown nonwoven fabric is highly efficient at filtering out particles, including PM2.5, dust, and bacteria. The carbon fiber cloth is durable and adds structural support to the fabric.The AC05-01 nonwoven activated carbon filter cotton has a weight of 250g per square meter and is available in various colors. The fabric has excellent air permeability, making it comfortable to wear for extended periods. It is also washable and reusable, making it an eco-friendly option compared to disposable alternatives.One of the main applications of this fabric technology is in the production of respiratory masks. The AC05-01 nonwoven activated carbon filter cotton can be used as the filter layer of masks to help protect the wearer from harmful substances in the air. With the rise of air pollution in many cities around the world, this technology offers a solution to help people breathe cleaner air.Besides masks, this fabric technology has other applications in various industries. It can be used in the production of air purifiers, car air filters, and even insoles for shoes. The ability to filter out harmful substances makes it a valuable addition to products that aim to improve indoor air quality.In conclusion, the introduction of nonwoven activated carbon filter cotton has opened up new possibilities in the fabric industry. Ruibang's AC05-01 product offers a high-quality solution to help protect people from the harmful effects of pollution. With its excellent filtering abilities and comfortable wear, it is sure to become a popular choice for those looking for functional fabrics.
New Carbon Fiber Cloth Technology: Stronger and more flexible than traditional materials
Cloth Carbon Fiber: A Game-Changer in the World of TextilesCarbon fiber has been steadily gaining popularity over the last few years, and for good reason. This durable, lightweight material has revolutionized many industries, including automotive, aerospace, and sports equipment. However, the world of textiles has been slower to adopt carbon fiber, due to the high cost and difficulty in manufacturing. That’s where Cloth Carbon Fiber comes in.Cloth Carbon Fiber is a company that specializes in producing high-quality carbon fiber textiles. Founded in 2010, the company has quickly become a leader in the industry, thanks to its innovative production methods and commitment to quality.One of the key features of Cloth Carbon Fiber’s textiles is their strength-to-weight ratio. Carbon fiber is incredibly strong, yet lightweight, making it an ideal material for textiles. This means that Cloth Carbon Fiber textiles are not only durable, but also very lightweight, making them perfect for a wide range of applications.The manufacturing process used by Cloth Carbon Fiber is also worth noting. Traditional carbon fiber production methods involve laying individual carbon fibers by hand, which is time-consuming and expensive. Cloth Carbon Fiber, on the other hand, uses an automated process that weaves the fibers together, greatly reducing production time and costs. This means that their carbon fiber textiles are more affordable and can be produced in larger quantities, making them more accessible to a wider range of customers.Cloth Carbon Fiber’s textiles have already made waves in the world of fashion and sportswear. Their carbon fiber fabrics have been used by designers to create unique, high-tech fashion pieces, and by athletic brands to create performance-enhancing clothing.But the applications for Cloth Carbon Fiber’s textiles extend far beyond fashion and sports. Carbon fiber’s strength, durability, and lightweight properties make it ideal for a wide range of applications, including construction, aerospace, and automotive.In the construction industry, Cloth Carbon Fiber’s textiles could be used to reinforce concrete structures, making them more resistant to earthquakes and other natural disasters. In the aerospace industry, carbon fiber is already widely used to make lightweight, yet strong components for planes and spacecraft. Cloth Carbon Fiber’s textiles could be used to create even more advanced components, helping to make space travel safer and more efficient.In the automotive industry, Cloth Carbon Fiber’s textiles could potentially revolutionize the way cars are made. Carbon fiber is already used in high-performance sports cars, but its high cost has made it impractical for mass-produced vehicles. However, Cloth Carbon Fiber’s more affordable textiles could change that, making it possible to create lightweight, fuel-efficient cars that are also durable and safe.Overall, the potential applications for Cloth Carbon Fiber’s textiles are vast and varied. Their innovative manufacturing process and commitment to quality have already established them as a leader in the industry, and their continued growth and expansion are sure to have a major impact on the world of textiles and beyond.
How Sewing Fiberglass Fabric Can Enhance Your DIY Projects
Title: Innovative Sewing Fiberglass Fabric Revolutionizes the Textile IndustryIntroduction:The textile industry is witnessing a groundbreaking innovation with the introduction of a remarkable sewing fiberglass fabric. Manufactured by an industry-leading company, this fabric is set to revolutionize various sectors, including automotive, aerospace, and construction. Offering exceptional strength, durability, and versatility, this cutting-edge material is poised to transform the way fabrics are used in diverse applications.1. Overview of the Sewing Fiberglass Fabric:The sewing fiberglass fabric, developed by a renowned company, combines advanced technology and meticulous craftsmanship to create a unique textile solution. With its distinct properties, this fabric surpasses traditional materials and offers numerous advantages across multiple industries.2. Strength and Durability:One of the key attributes of this sewing fiberglass fabric is its exceptional strength. Manufactured using a high-density fiberglass material, it provides exceptional tensile strength, making it ideal for applications that require resistance to heavy loads or extreme conditions.Moreover, the fabric enjoys remarkable durability, ensuring its longevity and reliability. Its robust composition enables it to withstand wear and tear, making it superior to conventional fabrics. These qualities make the sewing fiberglass fabric an unparalleled choice, particularly in industries where performance and longevity are crucial.3. Versatility in Applications:The introduction of this revolutionary sewing fiberglass fabric has opened up new possibilities in various sectors. In the automotive industry, it is being employed for the manufacturing of lightweight yet sturdy car seats, ensuring enhanced safety and comfort for passengers. Additionally, its application in vehicle upholstery offers exceptional resistance to fire and heat, further improving safety measures.Furthermore, the aerospace sector has recognized the potential of this fabric. Its unique combination of strength and lightweight properties makes it an ideal material for constructing aircraft interiors, including cabin panels and overhead storage compartments. By utilizing this fabric, aerospace manufacturers can reduce weight and improve fuel efficiency without compromising structural integrity.The construction industry also stands to benefit significantly from this remarkable fabric. Its high resistance to corrosive substances and extreme temperatures makes it suitable for reinforcing concrete structures, ensuring enhanced durability and longevity. Additionally, its application in the production of fire-resistant curtains or protective clothing for construction workers further adds to its versatility in this sector.4. Environmental Impact and Sustainability:The manufacturing process of this sewing fiberglass fabric adheres to strict environmental regulations, making it a sustainable alternative in comparison to other materials. Its longevity and robustness also contribute to reducing waste since it requires less frequent replacement. Moreover, its potential for recycling adds further value to its sustainability.5. Future Developments and Market Potential:The sewing fiberglass fabric is expected to witness extensive demand in the coming years. As the textile industry continues to focus on sustainability and innovative materials, this fabric's unique qualities make it a sought-after choice. The market potential is promising as major industries embrace the benefits it offers while seeking more efficient and eco-friendly solutions.Furthermore, ongoing research and development efforts are aimed at enhancing the fabric's properties, making it even more durable, lightweight, and cost-effective. Collaborations with other technology companies and fabric manufacturers are being explored to expedite the adoption of this fabric and explore new applications.Conclusion:The introduction of sewing fiberglass fabric marks a significant milestone in the textile industry. Offering unparalleled strength, durability, and versatility, this fabric has the potential to transform various sectors, from automotive and aerospace to construction. As its market potential grows and further advancements are made, this innovative fabric will continue to redefine the industry's standards, making it a cornerstone of textile manufacturing in the future.
High-Quality Unidirectional Carbon Fiber Fabric for Industrial Applications
Unidirectional Carbon Fiber Fabric: A Strong and Lightweight Solution for Various IndustriesIn today's world, technology has revolutionized the way we live our lives. Innovations in the manufacturing industry have paved the way for the development of new materials that are stronger, lighter, and more durable than conventional materials. One such material is Unidirectional Carbon Fiber Fabric, which has become increasingly popular in industries such as automotive, aerospace, sporting goods, and many others. Unidirectional Carbon Fiber Fabric is a composite material made up of strong carbon fibers that are tightly bonded together using a polymer matrix. The fibers in this material are unidirectional, meaning that they are all aligned in the same direction, which gives it its exceptional strength and stiffness. This material is preferred over traditional materials like steel and aluminum due to its high strength-to-weight ratio, which helps to reduce the weight of the final product while maintaining its structural integrity.In the automotive industry, Unidirectional Carbon Fiber Fabric is used extensively in high-performance sports cars, racing vehicles, and electric cars. The reduction in weight of these vehicles leads to improved fuel efficiency and better handling, resulting in a more enjoyable driving experience. The use of Unidirectional Carbon Fiber Fabric in car manufacturing helps to reduce carbon emissions, contributing to a sustainable future.The aerospace industry also benefits from the use of Unidirectional Carbon Fiber Fabric in aircraft design. The lightweight properties of this material make it ideal for aircraft manufacturing, leading to a reduction in fuel consumption and improved performance. The use of this material in aircraft manufacturing has enabled the development of new, innovative designs that are more aerodynamic and offer better performance.Sporting goods companies are also increasingly using Unidirectional Carbon Fiber Fabric to develop high-performance equipment such as tennis rackets, hockey sticks, and bicycles. The strength and stiffness of this material improve the performance of these products, giving athletes a competitive edge.It is worth noting that different industries require different types of Unidirectional Carbon Fiber Fabric, depending on their specific applications. The fabric’s strength and stiffness can be controlled by varying the direction of the carbon fibers, the type of polymer matrix used, and the density of fiber layers. As such, it is crucial to have a reliable supplier who can manufacture custom-made Unidirectional Carbon Fiber Fabric to meet the different needs of each industry.One such supplier is (**remove brand name**), a leading manufacturer of high-quality Unidirectional Carbon Fiber Fabric. The company has been in business for more than ten years, and during this time, it has established a reputation for excellence in quality, reliable customer service, and competitive pricing. (**Remove brand name**) uses state-of-the-art manufacturing technology to ensure that each product meets the highest industry standards. The company's in-house team of experienced engineers uses their expertise to develop custom-made Unidirectional Carbon Fiber Fabric that meets the specific needs of each customer.(**Remove brand name**) understands the importance of quality control and follows strict guidelines to ensure that all products meet the required standards. The company's products have been certified by various industry-standard organizations, including ISO 9001, ISO 14001, and OHSAS 18001. This ensures that customers can rely on (**Remove brand name**) for consistently high-quality products and exceptional service.In conclusion, the use of Unidirectional Carbon Fiber Fabric has opened up new avenues of innovation in various industries. The combination of strength, durability, and lightweight properties of this material makes it an ideal choice for manufacturing high-performance products. (**Remove brand name**) is a trusted name in the industry and is well-equipped to provide custom-made Unidirectional Carbon Fiber Fabric that meets the specific requirements of its customers. Through continuous innovation and quality control, (**Remove brand name**) is set to become a leader in the Unidirectional Carbon Fiber Fabric industry.
Discover the Promising Applications of Woven Glass Fabric in Today's News
Woven Glass Fabric Pushes Boundaries in the Textile Industry[Woven Glass Fabric Company] has recently unveiled their latest breakthrough in the field of textiles, a revolutionary product that is set to redefine the industry. Their cutting-edge woven glass fabric is set to push the boundaries of what is possible in textile manufacturing, offering a wide range of applications across various sectors. With unmatched strength, durability, and versatility, this innovative fabric is poised to transform industries and facilitate new possibilities in design and engineering.Woven glass fabric, also known as fiberglass fabric, is manufactured using threads made from glass fibers. These fibers are woven together to create a robust and flexible fabric that possesses exceptional properties. Woven glass fabric is known for its high tensile strength, which is significantly stronger than other fabrics such as cotton or polyester. This attribute makes it ideal for applications that require exceptional resilience, such as in the aerospace and automotive industries.What sets [Woven Glass Fabric Company]'s product apart from others in the market is their innovative manufacturing process. Using state-of-the-art technology and machinery, they have developed a technique that produces an incredibly fine yet durable woven glass fabric. This advancement allows for a higher level of detail and precision, making it a perfect choice for industries that demand stringent specifications.The versatility of this woven glass fabric is key to its success. Its ability to be molded into various shapes and sizes without compromising its structural integrity makes it incredibly appealing to designers and engineers. The fabric can be used in a vast array of applications, including but not limited to, insulation, filtration, reinforcement, and composite materials. The possibilities are truly limitless, and industries of all kinds are expected to benefit from this groundbreaking product.In the construction industry, woven glass fabric offers numerous advantages. Its exceptional strength-to-weight ratio makes it an ideal material for reinforcing concrete structures. It can also be used for insulation purposes, providing a more efficient and cost-effective solution compared to traditional insulation materials. Furthermore, woven glass fabric is resistant to corrosion, making it a durable option for a wide range of construction projects.The aerospace and automotive industries are also set to benefit greatly from this new textile innovation. The lightweight nature of woven glass fabric makes it an excellent choice for reducing overall weight in aircraft and vehicles, thereby improving fuel efficiency and performance. Its high strength also ensures the safety and integrity of critical components, making it an essential material in these high-demand sectors.Beyond its industrial uses, woven glass fabric also offers advantages in consumer products. The fabric can be used for creating high-performance sports equipment, such as tennis rackets or bicycle frames, due to its exceptional strength and flexibility. Additionally, it can be used in household applications, including furniture, curtains, and upholstery, providing a durable yet aesthetically pleasing option for consumers.[Woven Glass Fabric Company] has made significant investments in research and development, ensuring that their woven glass fabric remains at the forefront of the industry. They continuously strive to improve their manufacturing process, focusing on enhancing the fabric's properties while also minimizing its environmental impact. By prioritizing sustainability and innovation, [Woven Glass Fabric Company] aims to revolutionize the textile industry while also promoting responsible practices.The introduction of woven glass fabric marks a significant advancement in the textile industry. Its unparalleled strength, versatility, and durability offer numerous possibilities across various sectors. As [Woven Glass Fabric Company] pushes the boundaries of textile manufacturing, industries worldwide can look forward to the positive impact of this innovative fabric on their operations.
Exploring the Benefits of Carbon Fabric PrepregsCarbon fiber reinforced polymers are revolutionizing modern manufacturing by providing lightweight, high-performance material solutions for a wide range of applications. One of the most significant developments in this field is the production of Prepregs.Prepregs are a type of composite material that consists of a reinforcing fabric such as carbon, glass, or aramid (Kevlar) impregnated with a thermoset resin. This results in a ready-to-use composite material that can be easily formed into the desired shape and then cured to create a strong, durable, and lightweight part.Prepregs are produced by combining a reinforcing fabric and a thermoset resin system. The resin is typically in a B-staged state, meaning that it has been partially cured but remains tacky and can be handled without sticking to surfaces. This makes it easy to lay the fabric onto the sticky resin, which is then rolled to remove air bubbles and achieve an even distribution of the resin. The Prepreg is then packaged and stored in a cold environment to prevent the resin from fully curing.Carbon Fabric Prepregs have several advantages over traditional composite materials. First, Prepregs offer superior mechanical properties with high strength-to-weight ratios, which is a key characteristic of carbon fiber reinforced polymers. The reinforcing fabric provides the material with high strength and stiffness, while the resin system provides protection from environmental degradation and impact damage.Another significant benefit of Prepregs is their ease of use. Using Prepregs eliminates the need for expensive or complex tooling, as the material can be easily formed into the desired shape using common tools such as molds, rollers, and vacuum bagging. This reduces production time and costs, resulting in a more economical manufacturing process.Additionally, Prepregs enable increased design flexibility, as they can be customized to meet specific customer requirements. The choice of reinforcement fibers, resin systems, and manufacturing protocols can be optimized to suit the application and performance needs. This allows manufacturers to create parts that are tailored to their unique needs, resulting in more efficient and reliable products.Moreover, Carbon Fabric Prepregs are well-suited for a wide range of applications, including aerospace, automotive, marine, and sporting goods. Composites made from Prepregs are used in a variety of components, such as aircraft panels, automobile body parts, boat hulls, and bicycle frames. These applications benefit from the material's high strength-to-weight ratio, durability, and resistance to temperature and chemical degradation.In conclusion, Prepregs containing carbon fabric offer tremendous benefits to manufacturers looking for reliable and high-performance composite materials. The ease of use, increased design flexibility, and outstanding mechanical properties make Prepregs an ideal choice for a wide range of applications. Carbon Fabric Prepregs are changing the way manufacturers approach material selection, opening up new possibilities for lightweight, high-performance products that meet the needs of today's demanding markets.
High-Density 4.3 oz Prepreg Unidirectional Carbon Fiber Fabric for Marine Applications
Title: Harnessing the Power of 12k Carbon Fiber Fabric: The Versatile Solution for Marine ApplicationsIntroduction:Carbon fiber has revolutionized numerous industries with its exceptional strength, lightweight nature, and durability. In marine applications, where strength and performance are paramount, the utilization of carbon fiber becomes even more critical. Among various options, the 12k Carbon Fiber Fabric stands out due to its high density and unidirectional nature, ensuring maximum strength in a specific direction. This blog aims to explore the versatility and benefits of utilizing 12k Carbon Fiber Fabric in marine applications while highlighting its key features and addressing the importance of obtaining a high-density, non-woven fabric for optimal results.Understanding 12k Carbon Fiber Fabric:12k Carbon Fiber Fabric is a type of prepreg unidirectional fabric that boasts an incredibly high-density carbon fiber arrangement. The term '12k' represents the number of carbon filaments bundled together within a tow. Higher values indicate increased density, resulting in enhanced mechanical properties and strength. This fabric possesses the ideal characteristics to meet the demanding requirements of marine applications.Enhanced Strength & Durability:The primary goal of employing 12k Carbon Fiber Fabric in marine applications is to achieve maximum strength in a specific direction. The unidirectional nature of the fabric ensures that the fibers are aligned parallelly, allowing for exceptional stiffness and strength along that axis. This specific characteristic allows boat manufacturers to reinforce weaker sections and critical load-bearing structures effectively. The lightweight properties of carbon fiber minimize weight while maximizing structural integrity, further improving overall vessel performance.Corrosion Resistance and Longevity:One of the significant challenges faced by marine structures is corrosion due to constant exposure to harsh seawater environments. Traditional materials such as steel or aluminum are prone to corrosion and require regular maintenance. However, 12k Carbon Fiber Fabric possesses remarkable resistance to corrosion, making it an ideal choice for marine applications. With superior resistance to the elements, carbon fiber extends the longevity of marine structures, reducing maintenance requirements and ensuring prolonged performance.Applications in Marine Engineering:1. Hull Construction and Reinforcement:12k Carbon Fiber Fabric plays a crucial role in reinforcing and strengthening hull structures, offering unparalleled stiffness and rigidity. By integrating this fabric into the laminate or composite layers, boat manufacturers can enhance the overall structural integrity, ensuring exceptional performance, and reducing potential stress fractures in rough sea conditions.2. Masts, Booms, and Other Rigging Equipment:The unidirectional nature and strength of 12k Carbon Fiber Fabric make it an ideal material for building masts, booms, and rigging components. These critical structural elements require lightweight, yet rigid materials to withstand the forces exerted by wind and waves. Carbon fiber offers the perfect balance, allowing for reliable and high-performance rigging equipment.3. Bulb Keel Construction:When it comes to constructing bulb keels, 12k Carbon Fiber Fabric is the go-to option due to its remarkable stiffness and strength. Bulb keels significantly enhance the vessel's stability and maneuverability, and integrating carbon fiber fabric ensures maximum efficiency without adding unnecessary weight.Conclusion:The utilization of 12k Carbon Fiber Fabric in marine applications has opened up a world of possibilities for boat manufacturers, designers, and engineers. Its superior strength, lightness, corrosion resistance, and longevity make it an ideal choice for reinforcing various marine structures, including hulls, masts, booms, and bulb keels. With the ability to achieve maximum strength in one direction, 12k Carbon Fiber Fabric addresses the specific needs of marine engineering, ensuring exceptional performance even in challenging sea conditions. By leveraging the remarkable properties of this non-woven fabric, marine vessels are now capable of achieving new levels of strength, durability, and efficiency, contributing to the advancement of the industry as a whole.Keywords: 12k Carbon Fiber Fabric, prepreg unidirectional fabric, marine applications, maximum strength, high density, unidirectional nature, versatility, lightweight, durability, corrosion resistance, boat manufacturers, stiffness, rigidity, hull construction, masts, booms, bulb keel construction.
Fiberglass Cloth Roll: A Comprehensive Overview of 1708 Material
Title: Revolutionizing Reinforcements: Introduction of 1708 Fiberglass Cloth Roll in the Composites IndustryIntroduction (100 words):The composites industry has witnessed a game-changing development with the introduction of the innovative 1708 Fiberglass Cloth Roll. This groundbreaking product, manufactured by a leading company in the field, promises to revolutionize composites manufacturing with its exceptional properties and unmatched versatility. With a strong commitment to producing high-quality reinforcements, this company has once again proven its dedication to delivering cutting-edge solutions that exceed industry expectations. This article will delve into the details of the 1708 Fiberglass Cloth Roll, highlighting its remarkable features, benefits, and the significant impact it will have on various sectors that rely on composites for their operations.I. Overview of the 1708 Fiberglass Cloth Roll (200 words):The 1708 Fiberglass Cloth Roll represents a significant advancement in the field of composites reinforcements. It is a non-woven fabric made from continuous fiberglass roving that is laid flat and held together with a light binder. This unique manufacturing process ensures optimal conformity, durability, and strength.One of the most distinguishing features of the 1708 Fiberglass Cloth Roll is its combined axial and biaxial fabric orientation. This means that it consists of one layer of fiberglass roving aligned in the 0° (axial) direction and another layer placed at a 90° angle (biaxial). This configuration provides exceptional load-bearing capabilities in both direction orientations simultaneously, resulting in superior strength and stiffness for the composites it reinforces.Additionally, the 1708 Fiberglass Cloth Roll is compatible with a wide range of resin systems, making it adaptable to diverse manufacturing processes. Whether being utilized in wet lay-up, vacuum infusion, or hand lay-up techniques, this versatile reinforcement excels in enhancing the mechanical properties of various composite structures.Furthermore, the unique non-woven construction of the 1708 Fiberglass Cloth Roll offers improved wet-out characteristics, which ensures better resin distribution and ultimately enhances the bond between fibers and resin. This results in an optimal fiber-to-resin ratio, maximizing the performance and longevity of the composite product.II. Advantages and Applications (300 words):The introduction of the 1708 Fiberglass Cloth Roll carries numerous advantages, making it a highly sought-after reinforcement material in the composites industry. Some key benefits include:1. Superior strength and stiffness: The 1708 Fiberglass Cloth Roll ensures exceptional load-bearing capabilities, enhancing the overall strength and stiffness of composite structures. This makes it an ideal choice for various applications that require durable, lightweight materials.2. Versatility: The compatibility of the 1708 Fiberglass Cloth Roll with different resin systems and manufacturing processes allows for its use in diverse applications. It is widely employed in industries such as automotive, marine, aerospace, construction, and sporting goods.3. Improved wet-out characteristics: The non-woven construction of the 1708 Fiberglass Cloth Roll facilitates better resin distribution and adhesion, resulting in an optimal fiber-to-resin ratio. This significantly improves the performance and durability of composite products.4. Cost-effectiveness: By enhancing the mechanical properties of composites, the 1708 Fiberglass Cloth Roll helps manufacturers produce lightweight and durable products. This cost-effective solution reduces material waste and overall production costs.The application possibilities of the 1708 Fiberglass Cloth Roll are vast. In automotive manufacturing, it can be utilized in the fabrication of lightweight body panels, interior components, and structural parts, contributing to improved fuel efficiency and overall vehicle performance. In the marine industry, this innovation finds application in the production of hulls, decks, and bulkheads, ensuring superior integrity and longevity. The aerospace sector can benefit from the 1708 Fiberglass Cloth Roll in the construction of aircraft components, reducing weight while maintaining high strength and stiffness. In the construction industry, it finds use in building materials like structural panels, reinforcing beams, and columns, providing durability and resistance to environmental factors. Finally, the sporting goods industry can make use of this reinforcement material in the production of lightweight yet robust sporting equipment, enabling better performance for athletes.Conclusion (100 words):The introduction of the 1708 Fiberglass Cloth Roll marks a significant milestone in the composites industry. Its unique properties, versatility, and exceptional performance open up a world of possibilities for manufacturers across various sectors. With its superior strength, stiffness, and compatibility with different manufacturing processes, this reinforcement material has the potential to revolutionize composite manufacturing, enabling the production of lightweight, durable, and cost-effective products. As this innovative solution continues to gain momentum, it is clear that the 1708 Fiberglass Cloth Roll is set to become an indispensable tool for composites manufacturers in the years to come.